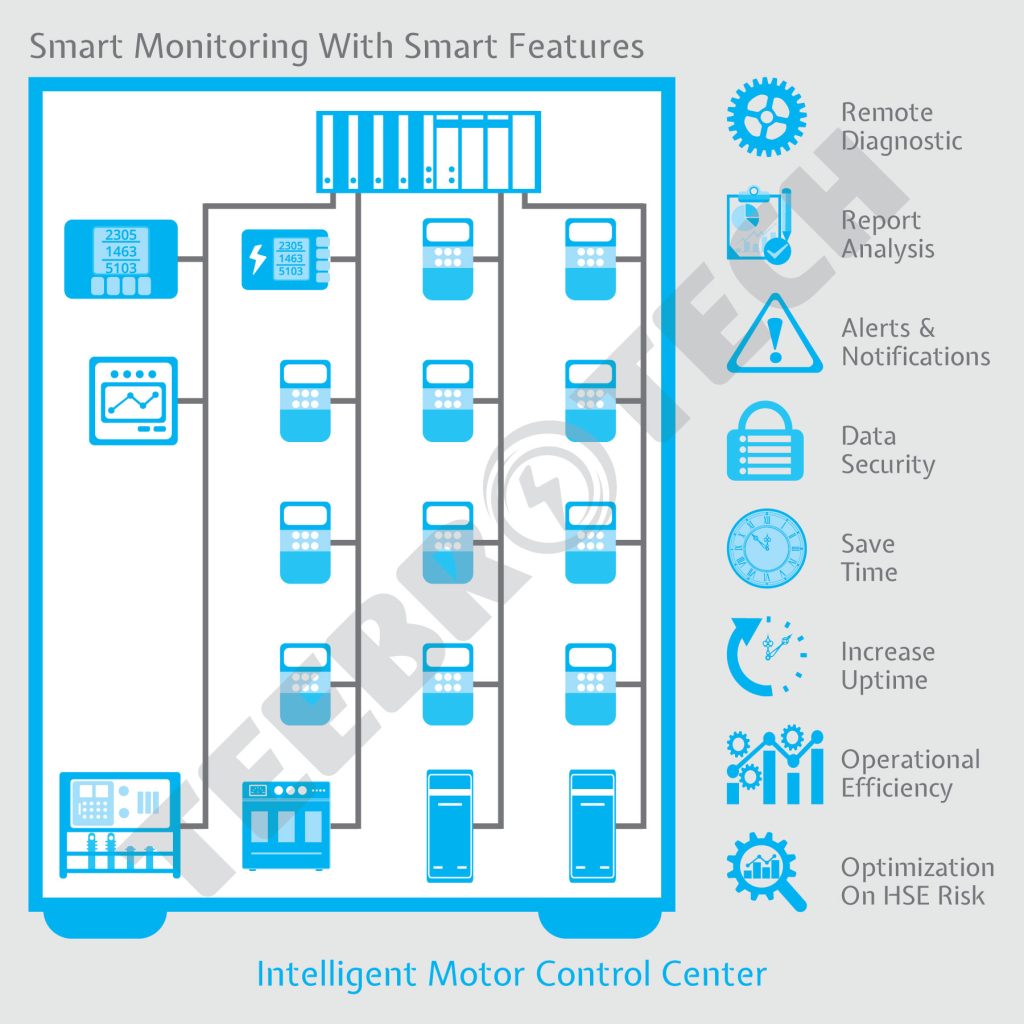
Motor Control Center Is Designed To Operate And Protect All The Connected Motors As Well As Related Switchgears In A Compact And Modular Way. The Very Basic Intention Is To Control The Motor Operation From A Single Location. So, All The Related Controls, Monitoring And Protective Electrical Devices Are Necessary For The Motor Feeder.
By Introducing Intelligent Motor Control Center, The Following Challenges Can Be Avoided –- Lot Of Wiring Compared To Conventional Control Centers.
- Installation Cost Can Be Reduced.
- No Option For Recording Or Visualizing Or Analyzing Fault Data; Hence, Unwanted Breakdown Happens On Regular Basis Which Actually Impacts On The Per Unit Production Cost
- Once The Unwanted Breakdown Happens, It Takes Much Longer Time To Troubleshoot The Fault Which Intern Affects The Production Capacity Heavily.
Conventional Motor Control Centers:
- CTs Are Mounted For Each Phase.
- Currents And Energy Are Monitored Through Each Motor On The Panel Only.
- CTs Are Wired With Thermal Or Electronic Overload Or Protection Relays.
- Most Of The Time, Conventional & Individual Switchgear & Protection Components Are Used Where Space Becomes As Issue.
- Lots Of Wiring To Incorporate All The Switchgear And Protection Components.
- Troubleshooting Is More Complex.
- Preventive Maintenance Is Difficult As The Fault Records Or History Are Not Available.

Intelligent Motor Control Centers:
- Intelligent Devices Along With Globally Accepted Industrial Communication Protocol Is Used To Control And Monitor All The Electrical Loads.
- Protections Such As Overload, Overcurrent, Instantaneous Overcurrent, Locked Current, Phase Failure, Phase Imbalance, Earth Faults Etc. Are Continuously Monitored As Well As Recorded Which Ultimately Ensure The Fast And Reliable Operation Plus Protection.
- Operational Data, Previous Recorded Data & Predictable Operational Data Can Be Analyzed Further To Avoid Unwanted Breakdowns And Plan For Preventive Maintenance.
- Remote Or Cloud Based Data Monitoring System Enables The Areas To Improve Further.
- As The Smart & Compact Switchgear & Protection Components Are Selected, Required Minimum Space To Install.
- Less Time Is Required To Install & Commission.
- Usually 10-15% Lower Installation Costs Compared To Conventional System.
- Simple And Flexible Compared To Conventional System.
- Provision To Extend Any System Any Time Without Any Hassle.
- Component Failure Rate Becomes Lower, The Overall System Life Space Becomes More.
- Finally, It Helps To Achieve The Overall Product Quality, Higher Product Availability & Equipment Effectiveness.